Innovative biomethane technologies
on a smaller scale: a feasible case
Biogas-E Case Study 3 Interview
The Net-Zero Industry Act (NZIA) supports innovation through regulatory sandboxes that allow net-zero technologies to be tested in a controlled environment before being marketed. This instrument improves the learning process in terms of regulations and possible upscaling, and fits seamlessly with the SEMPRE-BIO case studies that investigate sustainable innovative biomethane technologies. One of these case studies is located on the dairy farm De Zwanebloem in Adinkerke and aims to transform organic waste into bio-LNG and liquid CO2 on a smaller scale.
De Zwanebloem’s main role is the biogas supply. Cryo Inox is responsible for the implementation and operation of the cryogenic installation. Ghent University coordinates the Flemish demo site and is thus in charge of general management and monitoring. They are in close contact with Innolab and Biogas-E. Ghent University is also involved in the valorization of by-products, such as digestate and CO2.
Biogas-E interviewed Wannes Masscheleyn, managing director of De Zwanebloem and Çağrı Akyol, postdoctoral project manager and researcher at Ghent University.
Hello Wannes, can you tell us more about your farm in Adinkerke?
Wannes: De Zwanebloem is a family business in dairy farming. We currently milk 900 cows. In addition to milk, the cows also produce about 35,000 tonnes of manure per year. Until recently, manure was applied to our own and neighboring fields. We have two anaerobic digesters, one mesophilic and one thermophilic, in which we can process 25,000 tonnes of manure and 5,000 tonnes of co-substrates (e.g. Corn Cob Mix) annually. These digesters are now one month operational. A CHP with a capacity of 435 kWe valorizes the produced biogas into green electricity and heat that we can use ourselves. Within the SEMPRE-BIO project, the biogas will temporarily be used for the production of bio-LNG and liquid CO2 via cryogenic separation.
Why did you choose for anaerobic digestion?
Wannes: We are obliged to process 15,000 tonnes of manure every year. When we heard that digestate resulting from thermophilic digestion may be transported to France, this seemed like a good opportunity given our location near the border. Moreover, through anaerobic digestion we can reduce our electricity costs and obtain certificates, which is economically more beneficial than sending manure to biological processing.
What is innovative about the technology being researched within SEMPRE-BIO?
Çağrı: On the one hand, cryogenic separation is not that common for biogas upgrading. On the other hand, biogas upgrading mainly takes place on a larger scale in other countries. Therefore, the reduction in scale of this technology is innovative.
What were/are the bottlenecks when installing the digesters and the upgrading installation?
Wannes: The biggest challenge is obtaining the permit, mainly because of the nitrogen problem in Flanders. The safety aspects linked to bio-LNG production may also cause some challenges. The permit application for the biomethane upgrading facility is currently being finalized. The application for digestate transport to France is ongoing.
“The biggest challenge is obtaining the permit, mainly because of the nitrogen problem in Flanders.”
Was this in line with your expectations and can we learn something from this for the future?
Wannes: Before the start of the project, we already had discussions with the delegation in Bruges. They were quite positive as the number of cattle remains unchanged in the permit and therefore there is no effect on the company’s general nitrogen emissions. At first, it seemed that a notification would be sufficient. Ultimately however, a permit application turned out to be necessary. More frequent use of such or similar technologies could simplify the permitting process, although there are of course many company-specific factors to take into account.
Furthermore, the legislation applicable in the future plays a major role. Allowing everything to take its course may result in a natural decline in livestock numbers, but it must be realized that this will no longer result in an influx of new farmers and could possibly lead to shortages of our basic products in the near future.
Can NZIA provide a boost?
Wannes: It is positive that European legislation exists to simplify the application of innovative technologies. However, practice shows that translation of European legislations to Member State level is often difficult and that there is too little standardization. In fact, border policy in general is a bottleneck that needs to be addressed first. Border policy between Flanders and Wallonia is already quite a challenge.
Çağrı: We are often still very dependent on countries outside Europe. Much of the renewable energy equipment, also for biogas and biomethane production, is imported from China. This can have several disadvantages, including production problems, quality control issues, or unexpected costs. The positive thing is that local and regional production is increasingly stimulated, partly by the NZIA.
“We are often still very dependent on countries outside Europe.”
What about the future of innovative biogas and biomethane production technologies?
Çağrı: Interest in biogas, biomethane and associated technologies is growing. Biogas and biomethane are very versatile and can be used in a flexible way. One of the main reasons for the increasing interest is the conflict between Russia and Ukraine, which clearly showed how dependent Europe is on Russian natural gas. If this trend continues, the biomethane target set by the EU in the REPowerEU plan certainly seems feasible, provided that the challenges linked to the application of digestate (products) are also addressed.
Wannes: Our milk collection trucks currently run on LNG. In an ideal circular scenario, bio-LNG could be used in these trucks and also in our tractors. The application of bio-LNG in heavy transport is currently still very rare in Flanders. This makes it more difficult to take the (first) step.
Are there any other innovations planned?
Wannes: The next step is to find a way to remove the nitrogen from the air in the stables. There are many interesting innovations, but these are often not profitable on a smaller scale due to the high investment costs. The Flemish government must also give us the necessary room for innovation. This is currently a limiting factor, also for example with regard to the use of a nitrogen stripper and algae in animal feed.
“The Flemish government must also give us the necessary room for innovation.”
Also discover the other two case studies from Spain and France:
- small-scale biogas-to-biomethane installation, with combination of CO2 biomethanation and PEM electrolysis
- small-scale (wood) waste-to-biomethane installation, with combination of pyrolysis and syngas biomethanization, with purification to biomethane
More information on the SEMPRE-BIO project website.
Author: © Biogas-E magazine
Date: August, 2024
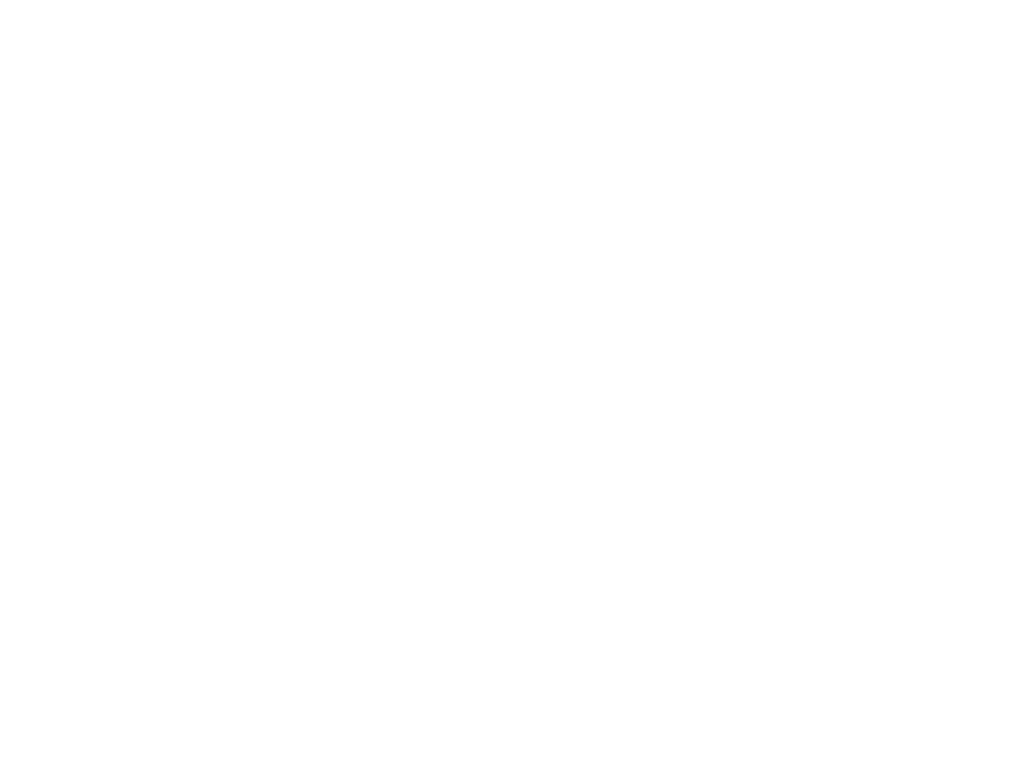
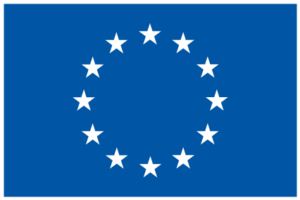
This project has received funding from the European Union’s HORIZON-CL5-2021-D3-03-16 program under grant agreement No 101084297. Views and opinions expressed are however those of the author(s) only and do not necessarily reflect those of the European Union or the European Commission. Neither the European Union nor the granting authority can be held responsible for them.